Whether you are the owner of a small organization or part of a large organization, it is mandatory to have a scheduled maintenance plan in place. The type of maintenance you adopt will depend on the kind of equipment you own, the skill level of your workers, your budget, and the complexity of your operations.
If you have sophisticated and expensive equipment that is critical for your operations, it would be wise to invest in predictive maintenance. Assets that are not so critical can be managed with routine maintenance. You might need different types of maintenance for your workplace.
Let us find out the different types of maintenance and their applications.
Different Types Of Maintenance
Maintenance definition describes it as the scheduled checking of equipment, machinery, and related infrastructure in commercial or residential units including any repairs and replacement of parts.
Now that the definition of maintenance is clear, here are the different types of maintenance –
Preventive Maintenance
This belongs to the category of planned or proactive maintenance. You would require cmms software for implementing preventive maintenance.
The core idea of preventive maintenance is checking equipment for repairs or replacement based on a schedule. The condition of the equipment is not important here. If a quarterly maintenance schedule is planned, then the equipment will be examined every quarter.
The benefits of preventive maintenance include lowering downtime of equipment that occurs due to reactive maintenance and increased lifespan of the asset. It prevents equipment failure by checking the asset for wear and tear of parts and replacing the asset when required. You save on costs of emergency repair and frequent replacement of critical assets.
Preventive maintenance enables compliance with OSHA standards and ensuring higher workplace safety. When your assets are in optimal working condition, you get improved efficiency and better resale value.
The drawback of preventive maintenance is the downtime due to time-based scheduling rather than need-based scheduling.
Predictive Maintenance
Unlike preventive maintenance, predictive maintenance is scheduled based on the condition of the asset and not according to a pre-set frequency. Real-time data from the asset is obtained through sensors and is used to determine when maintenance is due next. The asset is replaced before the breakdown stage.
The predictive maintenance process starts with defining baseline parameters before sensors are installed. Any deviation from the parameters triggers the sensors and the technicians are altered through the work order. Predictive maintenance provides higher efficiency with lower downtime compared to preventive maintenance.
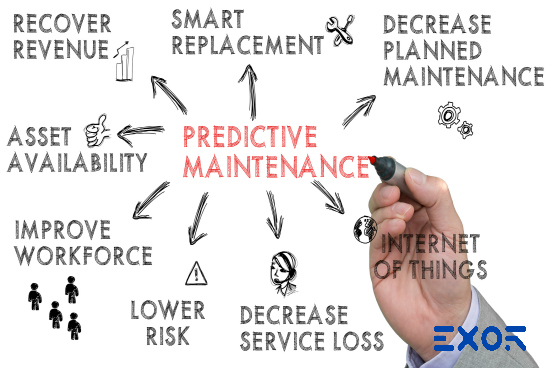
However, implementing predictive maintenance is time-consuming due to the technology involved, integration with your existing software, and requires a shift from your existing company culture. You need to train your technicians or hire trained technicians for predictive maintenance but the benefits outweigh the costs.
Routine Maintenance
Like preventive maintenance, routine maintenance follows a schedule based on a certain frequency. The condition of the asset is not important. The frequency of routine maintenance is higher compared to preventive maintenance and is used for less complex tasks like cleaning unlike inspections carried out under preventive maintenance.
The reason for routine maintenance being adopted by most organizations is its simple application. You don’t need trained staff to carry out routine maintenance, it can be performed by janitors or operators. Predictive maintenance is classified as non-routine maintenance since it depends on the condition of the asset.
Condition-Based Maintenance
Though the concept of condition-based maintenance is similar to predictive maintenance, the results may not be as accurate as of the latter. Its core idea is that maintenance is triggered when a specific condition is fulfilled. It might be more effective than predictive maintenance in cases where trained operators know what possible problems might arise.
Planned Maintenance
Though preventive maintenance is a type of scheduled maintenance, it is not planned maintenance. The latter requires the technician is ready for the task with the skills, spare parts, and other requirements within the given timeframe.
Emergency Maintenance
Unlike planned maintenance, this type of maintenance is unplanned. It falls in the reactive maintenance category and disrupts production flow. It is the major cause of downtime since the repairs or spare part replacements take place after the equipment has failed.
Other drawbacks of emergency maintenance include compromise with workplace safety and failure to comply with OSHA standards.
Corrective Maintenance
This category can also be classified as emergency maintenance since it takes place when something needs correction or fixing. It can also be used proactively since the action can be taken when there is feedback from the sensors used in predictive maintenance. However, predictive maintenance is normally undertaken when the asset is functioning efficiently.
Failure Finding Maintenance
There are certain equipment parts like pressure safety valves that play a protective role. The challenge with detecting the failure of such equipment is that it can’t be detected unless the primary component of the asset fails.
You have to find these hidden failures before you can safely use the asset. Detecting the failure is not enough, you need to repair it. This type of maintenance needs to be conducted at regular intervals.
Risk-Based Maintenance
Under this method of maintenance, assets are classified according to how critical they are for the production process and the probability of failure. Critical assets with a high risk of failure are given the top priority. Your maintenance technicians would spend the most time on these critical assets.
This is a highly efficient process of maintenance since the total impact of the failure is the least with critical assets receiving the most attention and low-risk assets the least attention. Risk assessment is a continuous process and is a form of preventive maintenance. The assets are color-coded based on risk making it easier for maintenance.
Final Thoughts
The right type of maintenance makes the difference between business success and failure. If you feel your business cannot afford high-level maintenance like preventive maintenance or predictive maintenance, then you can start with routine maintenance.
Maintenance of equipment for workplace safety is mandatory as per regulations like OSHA. Failure to comply with these regulations could result in severe penalties. You need to ensure that safety warnings are displayed prominently so that technicians can follow them.
With scheduled maintenance or condition-based maintenance, your equipment is in peak condition and has a longer life. Your profits are higher since the assets experience maximum uptime.
Analyze your current business requirements and implement the required maintenance program. With long-term savings in terms of minimal equipment failure and higher profits, your organization will reach greater heights.
Leave a Reply